-
• ReSL established and operates a facility dedicated to the destruction of pure PCB and PCB-contaminated oil, along with Sludge Dispersion for low-level PCB treatment.
-
• The state-of-the-art facility employs cutting-edge Plascon and Indirect Thermal Desorption (ITD) technologies for efficient and safe PCB waste management.
-
• The facility, with a processing capacity of 330 tons of PCB waste annually, achieves Zero Liquid Discharge (ZLD) by treating and recycling all wastewater within the plant.
The Global Environment Fund (GEF) supported a project to promote the environmentally sound management and safe disposal of Polychlorinated Biphenyls (PCBs) in India. The Bhilai Steel Plant of SAIL was selected as the primary beneficiary. The initiative was backed by the Ministry of Environment, Forest, and Climate Change (MoEF&CC) and implemented by the United Nations Industrial Development Organization (UNIDO)
PCBs are synthetic chemicals widely used in industrial and consumer applications, including insulation fluids for transformers and generators, fluorescent lamp ballasts, caulk, and carbonless copy paper. However, due to their classification as “probable human carcinogens” and their identification as hazardous pollutants under the Stockholm Convention on Persistent Organic Pollutants (2001), the management of PCBs requires stringent and environmentally sound measures.
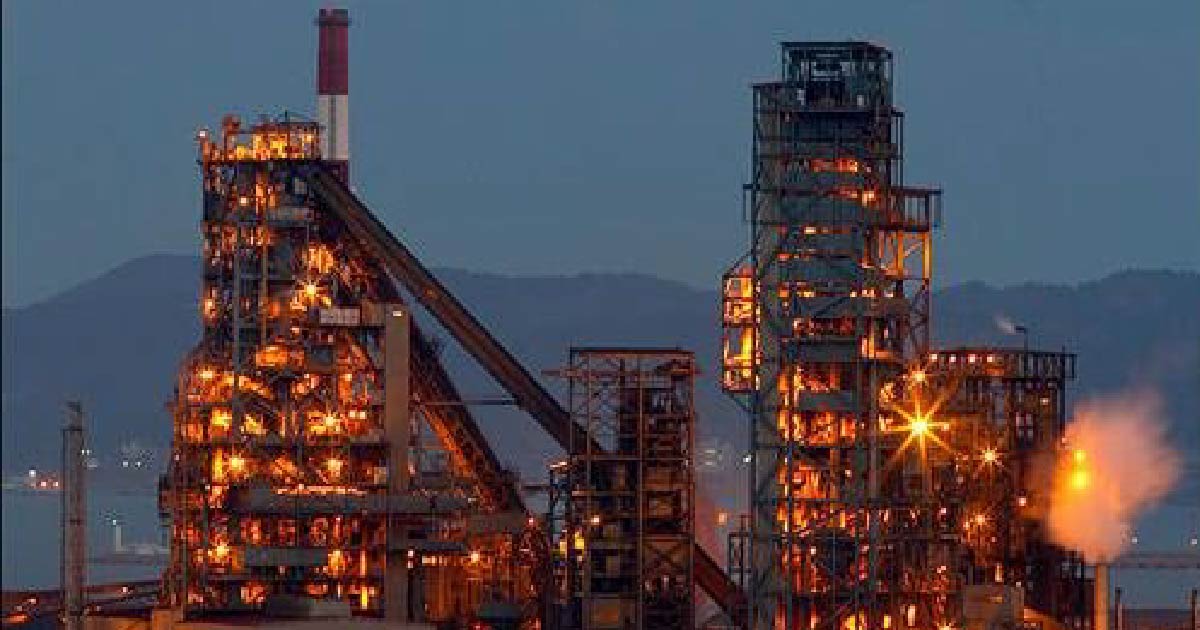
Bhilai Steel Plant engaged Re Sustainability Limited (formerly Ramky Enviro Engineers Limited) to establish and operate a dedicated facility for PCB management. Operational since December 2022, the facility is equipped to destroy pure PCB liquid waste, decontaminate porous materials contaminated with PCBs, and manage PCB-contaminated oils and wastes. With a capacity to process 330 tons of PCBs annually, the plant employs advanced technologies such as Plascon and an Internal Thermal Desorption system to ensure efficient destruction and decontamination. Transformers received at the facility are drained of oil and dismantled, and all hazardous waste generated during operations is responsibly managed through scientific landfilling. As a Zero Liquid Discharge (ZLD) facility, it exemplifies sustainable and compliant hazardous waste management.
By integrating advanced technologies and sustainable practices, it sets a benchmark for hazardous material management and supports a cleaner, safer future.
- Zero Waste